Vakuumguss Prototypen & Kleinserien – schnell & präzise fertigen
Lernen Sie die Vorteile des Vakuumgussverfahrens für die schnelle und kostengünstige Herstellung von Prototypen und Kleinserien kennen. Vertrauen Sie auf hohe Detailgenauigkeit und vielseitige Materialauswahl für Ihre Projekte.
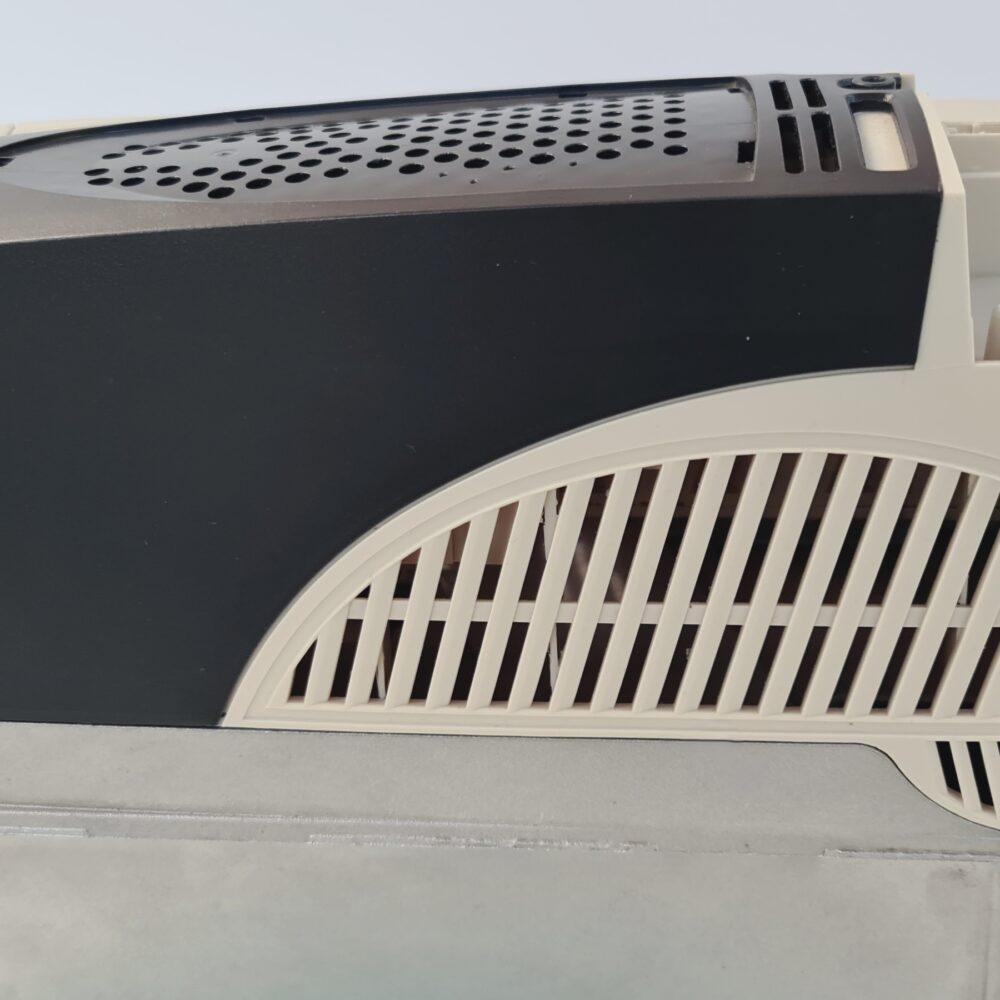
Was ist Vakuumguss?
Das Vakuumgießverfahren ist eine bewährte Methode zur schnellen und kosteneffizienten Herstellung von Prototypen und Kleinserien. Mit Silikonformen und hochwertigen Polyurethanharzen entstehen Bauteile mit hoher Detailgenauigkeit und exzellenter Oberflächenqualität.
Funktionsweise:
Zunächst wird ein Urmodell erstellt – meist per 3D-Druck oder manuelle Fertigung. Dieses Modell wird in Silikon eingebettet, wodurch eine Negativform entsteht. In dieser Form werden die flüssigen Harze unter Vakuum blasenfrei vergossen.
Dank unseres modernen Differenzdruck-Systems lassen sich auch sehr zähflüssige Materialien zuverlässig verarbeiten. So können neben Polyurethanen auch Silikone eingesetzt werden, was eine große Bandbreite an Eigenschaften ermöglicht.
Materialien:
Zunächst wird ein Urmodell erstellt – meist per 3D-Druck oder manuelle Fertigung. Dieses Modell wird in Silikon eingebettet, wodurch eine Negativform entsteht. In dieser Form werden die flüssigen Harze unter Vakuum blasenfrei vergossen.
Dank unseres modernen Differenzdruck-Systems lassen sich auch sehr zähflüssige Materialien zuverlässig verarbeiten. So können neben Polyurethanen auch Silikone eingesetzt werden, was eine große Bandbreite an Eigenschaften ermöglicht.
Typische Anwendungen:
Das Verfahren wird in vielen Branchen genutzt, darunter:
- Automobilindustrie (Innen- & Außenteile, Funktionsprototypen)
- Medizintechnik (Gehäuse, Funktionsmuster)
- Elektronik & Konsumgüter (Designmodelle, Kleinserien)
Auch beim Reverse Engineering ist Vakuumgießen im Einsatz, z. B. wenn Ersatzteile nicht mehr verfügbar sind und kurzfristig reproduziert werden müssen.
Vorteile gegenüber Spritzguss
- Keine hohen Werkzeugkosten – ideal für Kleinserien
- Sehr gute Oberflächenqualität ohne Einfallstellen
- Kurze Lieferzeiten dank schneller Formherstellung
- Hohe Materialvielfalt durch PU- und Silikonharze
Damit kombiniert das Verfahren die Flexibilität des Rapid Prototyping mit der Qualität seriennaher Fertigung – perfekt für Entwicklung, Funktionstests und Kleinserienproduktion.
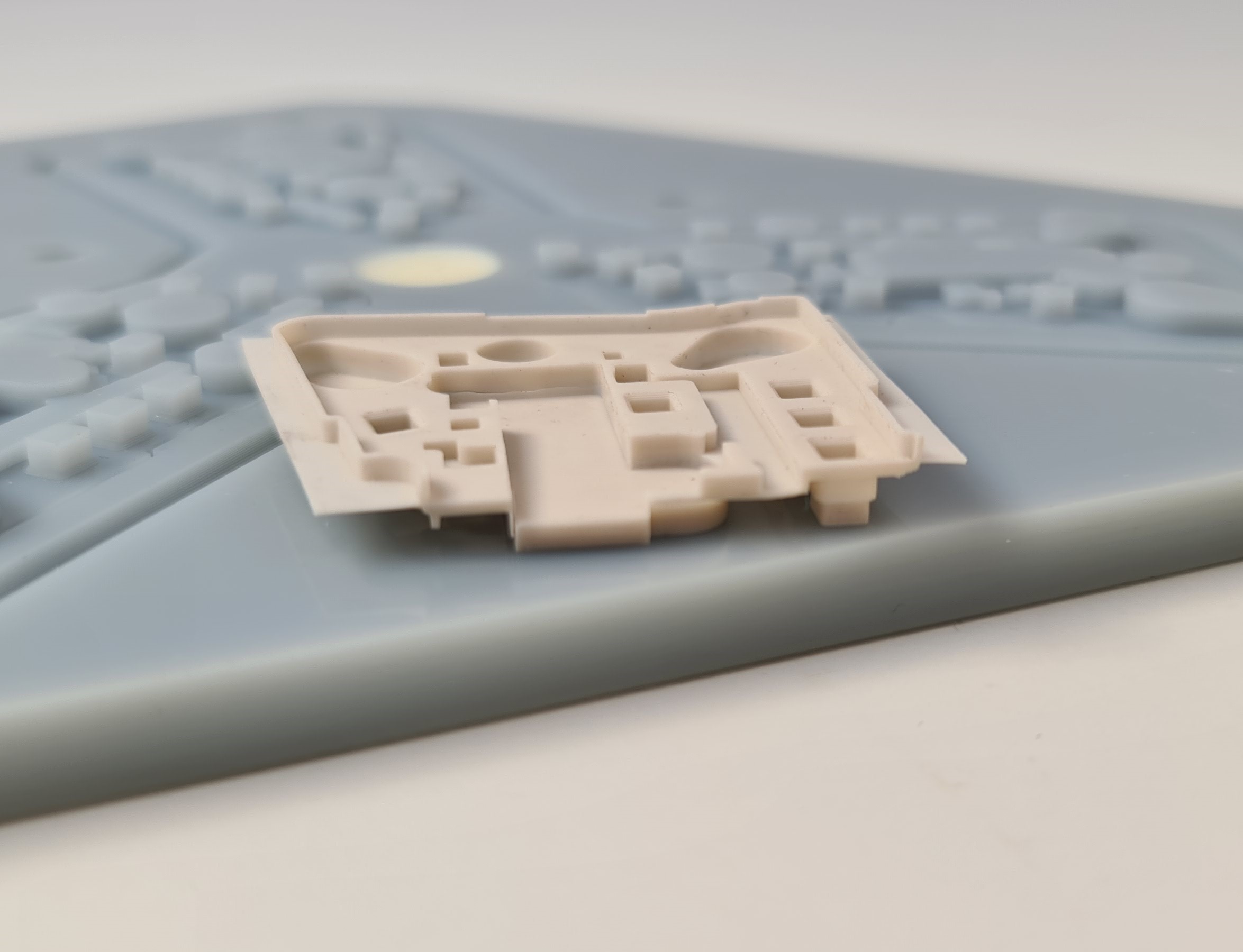
Erfahren Sie mehr über die Vorteile von Vakuumguss
Hohe Detailgenauigkeit
Mit dem Vakuumgießverfahren lassen sich auch komplexe Geometrien und feine Details präzise abbilden.
Vielseitige Materialauswahl
Es stehen zahlreiche Werkstoffe zur Verfügung – von Polyurethanharzen bis zu Silikonen – für individuelle Anforderungen.
Flexibilität in Shore-Härten
Materialien in verschiedenen Härtegraden machen die Fertigung vielseitig einsetzbar, vom weichen Prototyp bis zum robusten Funktionsteil.
Wenig Nachbearbeitung
Die präzisen Formen und hochwertigen Harze reduzieren den Aufwand für Nacharbeit deutlich.
Serienfähige Oberflächenqualität
Die präzisen Formen und hochwertigen Harze reduzieren den Aufwand für Nacharbeit deutlich.
Ablauf des Vakuumgiessverfahrens bei Waltl Design
Der Vakuumgussprozess bei Waltl Design ist effizient und präzise, um höchste Qualitätsstandards zu gewährleisten.
- Erstellung des Urmodells (Mastermodell) durch 3D-Druck oder handgefertigte Modelle.
- Fixierung des Urmodells in einem Formkasten und Befüllung mit flüssigem Silikon.
- Aushärtung des Silikons und Entnahme des Urmodells aus der Negativform.
- Produktion der Bauteile durch Befüllung der Silikonform mit spezifischen Polyurethanharzen unter Vakuum.
- Aushärtung und Nachbearbeitung der Bauteile.
- Entgraten und Endkontrolle
Sie Provitieren bei uns
Bei uns profitieren Sie von einer schnellen, präzisen und wirtschaftlichen Fertigung. Ob Prototyp oder Kleinserie – wir setzen Verfahren ein, die hohe Flexibilität bei Materialien, Detailgenauigkeit und Oberflächenqualität ermöglichen
Die 6‑stufige Waltl-Design-Methode: Der Weg zu Ihrem perfekten Produkt
Gewinnen Sie Kenntnisse darüber, wie wir in 6 Schritten aus Ihrer ersten Idee ein serienreifes Produkt entwickeln. Das 6‑stufige Rundumpaket bietet Ihnen eine individuelle Beratung in allen Phasen und hilft Ihnen, externe Kosten einzusparen.
Mehr Erfahren Kontakt aufnehmenJedes Projekt ist anders – und genau darin liegt unsere Stärke.
Mit einem breiten Spektrum an Fertigungsmöglichkeiten und einem Gespür für individuelle Anforderungen entwickeln wir Lösungen, die wirklich passen. Schnell, flexibel und persönlich.
FAQ – Häufige Fragen zum Vakuumgussverfahren bei Waltl-Design
Was ist Vakuumguss?
Vakuumguss (auch Vakuumgießen oder Vakuumguß) ist ein Fertigungsverfahren zur Herstellung von Prototypen und Kleinserien. Dabei wird flüssiges Material – meist Polyurethanharz – unter Vakuum in eine Silikonform gegossen.
Durch das Unterdruckverfahren werden Luftblasen und Hohlräume vermieden, sodass hochwertige Bauteile mit feiner Detailgenauigkeit und glatter Oberfläche entstehen.
Welche Materialien werden im Vakuumguss verwendet?
Im Unterdruckguss kommen vor allem Polyurethanharze (PU) zum Einsatz. Diese lassen sich in unterschiedlichen Shore-Härten einstellen – von weich und elastisch bis hin zu hart und robust.
Je nach Anforderung können auch Silikone oder vergleichbare Kunststoffe verarbeitet werden. Damit eignet sich das Verfahren für funktionsnahe Prototypen und langlebige Kleinserien in verschiedensten Branchen.
Wie läuft der Kleinserienguss im Vakuumverfahren ab?
Der Prozess beginnt mit der Herstellung eines Ur-Modells, das meist mittels 3D-Druck erstellt wird. 2K Platinsilikon wird um das Modell gegossen und nach der Aushärtung mittels Skalpells aufgeschnitten und das Urmodell entfernt. Die Form kommt dann in eine Vakuumkammer, wo das flüssige 2K Polyurethan eingefüllt wird. Das Bauteil härtet nach dem Befüllen im Ofen bei ca. 60°C aus.
Welche Eigenschaften machen Vakuumguss-Bauteile so attraktiv?
Prototypen und Kleinserien:
Hohe Präzision & Detailtreue – selbst komplexe Geometrien und feine Strukturen können exakt abgebildet werden.
Schnelle & kosteneffiziente Fertigung – ideal für Kleinserien und Prototypen, ohne hohe Werkzeugkosten.
Vielfältige Materialauswahl – von flexiblen bis hochfesten Polyurethanharzen und Silikonen, in verschiedenen Shore-Härten.
Seriennahe Qualität – Bauteile wirken wie im Spritzguss gefertigt und sind perfekt für Funktionstests oder Designbewertungen.
Individuelle Farboptionen – nahezu alle RAL-Farben, transparente oder transluzente Varianten sind möglich.
Wie lange dauert der Vakuumgussprozess?
Die Dauer des Vakuumgussprozesses kann variieren, je nach Komplexität des Teils und der Anzahl der benötigten Teile. In der Regel dauert die Herstellung einer Silikonform einige Stunden, während das eigentliche Gießen und Aushärten des Materials in wenigen Stunden bis zu einem Tag abgeschlossen sein kann.
❓ Wo liegen die Grenzen im Vakuumgießen?
Das Vakuumgießverfahren eignet sich hervorragend für Prototypen und Kleinserien. Pro Form lassen sich in der Regel 25 bis 40 Bauteile fertigen. Wirtschaftlich ist das Verfahren bis zu einer Größenordnung von etwa 500–1.000 Stück.
In beiden Verfahren – Vakuumgießen und Spritzguss – steht eine sehr gute Materialauswahl zur Verfügung. Beim Spritzguss ist die Bandbreite für Großserien noch größer, weshalb er dort bevorzugt eingesetzt wird.
Eine Gemeinsamkeit: helle Farben können in beiden Verfahren mit der Zeit leicht vergilben.
❓ Brauchen unsere Bauteile eine Nachbearbeitung?
❓ Brauchen unsere Bauteile eine Nachbearbeitung?
In den meisten Fällen sind keine zusätzlichen Oberflächenbehandlungen erforderlich. Das liegt daran, dass die Silikonform die Oberflächenqualität des Urmodells exakt übernimmt.
Auf Wunsch sind jedoch verschiedene Nachbearbeitungen möglich:
Schleifen
Polieren
Lackieren oder Beschichten – für Farbgebung, Schutz oder spezielle Eigenschaften
👉 Zusätzlich können die Bauteile schon vor dem Lackeiervorgang eingefärbt werden. So bleiben auch bei späteren Kratzern keine Farbunterschiede sichtbar.
❓ Warum eignet sich Vakuumguss für Kleinserien?
Das Vakuumgießverfahren ist eine kosteneffiziente Alternative zum Spritzguss, wenn nur kleine Stückzahlen benötigt werden. Da keine teuren Metallwerkzeuge erforderlich sind, sinken die Herstellungskosten deutlich.
Gleichzeitig bieten die Bauteile eine hohe Stabilität, glatte Oberflächen und lange Lebensdauer – ideal für funktionsfähige Prototypen und Kleinserien.
Beauftragen Sie uns für Ihr Vakuumguss-Projekt!
Interessiert an unseren Vakuumguss-Dienstleistungen? Unser Team steht Ihnen mit umfassender Beratung und erstklassigem Service zur Seite. Lassen Sie uns gemeinsam Ihre Ideen verwirklichen.
Nehmen Sie jetzt Kontakt mit uns auf!
Zum Kontaktformular