Faserverbund
(CFK/GFK) für Prototypen & Serienfertigung
Wir fertige Bauteile aus Faserverbundwerkstoffen (CFK/GFK) – leicht, stabil und belastbar. Ideal für Prototypen, Vorserien und Serienfertigung. Faserverbund hat einen hohen Stellenwert in Luft- & Raumfahrt, Automobilbau und Medizintechnik. Fertigung in Deutschland, Fokus Bayern & Baden-Württemberg.
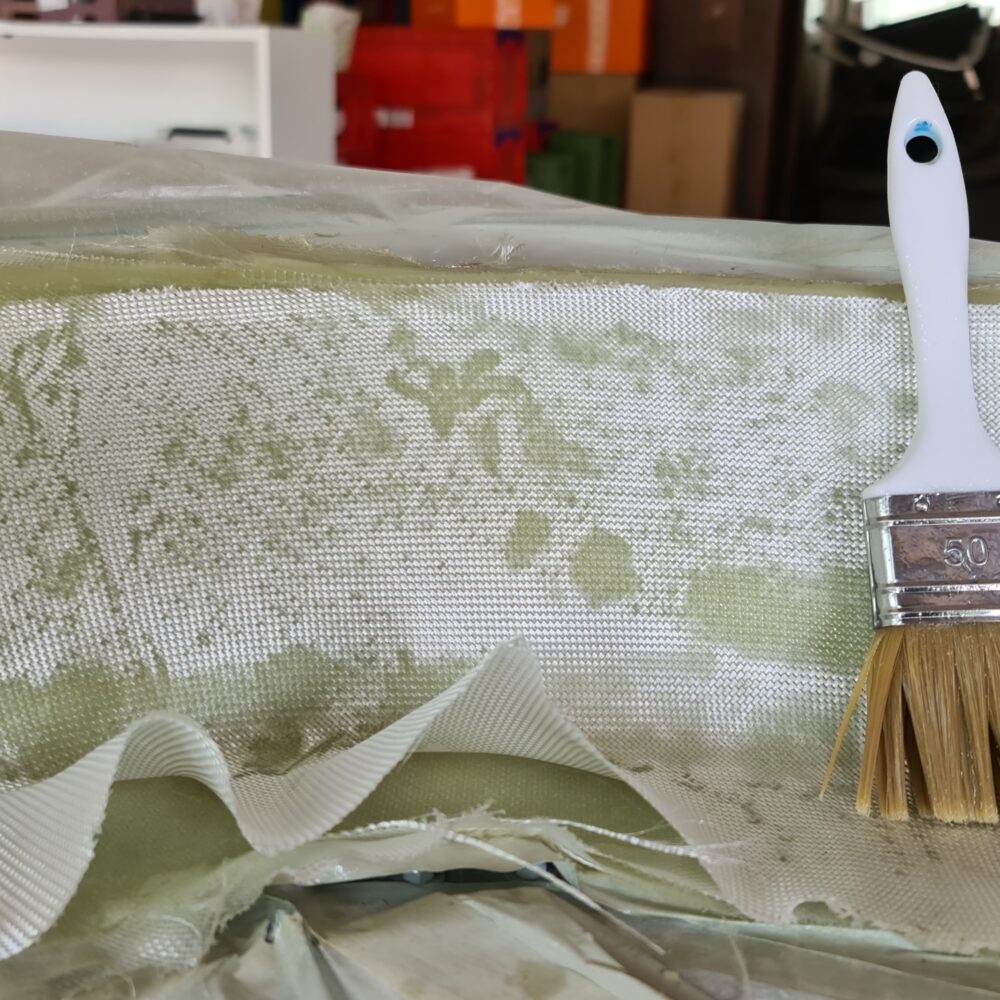
Einsatzbereiche von Faserverbund
Faserverbund (CFK/GFK) hat sich in vielen Branchen bewährt. Leichtbau und Stabilität sind entscheidend – egal ob in Prototypen oder Serienfertigung. Besonders in Luft- und Raumfahrt, Automotive, Medizintechnik und Maschinenbau werden CFK- und GFK-Bauteile täglich eingesetzt.
Nischen mit großem Potenzial
„Auch kleinere Märkte profitieren: Sportgeräte, Drohnen, Robotik oder Designprodukte. Hier ermöglicht Faserverbund hohe Leistungsfähigkeit bei geringem Gewicht. Für Start-ups oder Spezialanwendungen biete wir Beratung und Musterteile, um schnell marktfähige Produkte umzusetzen.
Was ist Faserverbund?
Faserverbund (CFK/GFK) hat sich in vielen Branchen bewährt. Leichtbau und Stabilität sind entscheidend – egal ob in Prototypen oder Serienfertigung. Besonders in Luft- und Raumfahrt, Automotive, Medizintechnik und Maschinenbau werden CFK- und GFK-Bauteile täglich eingesetzt.
Definition und Zusammensetzung
Faserverbundwerkstoffe, oft einfach als Verbundmaterialien bezeichnet, bestehen aus zwei oder mehr verschiedenen Materialien, die kombiniert werden, um die Vorteile jedes einzelnen Materials zu nutzen. Die typische Zusammensetzung umfasst eine Matrix, meist ein Polymerharz, und eine Verstärkung durch Fasern wie Kohlenstoff‑, Glas- oder Aramidfaser. Diese Kombination führt zu Materialien, die sowohl leicht als auch außerordentlich stabil sind.
Anwendungsbereiche und Vorteile
Durch die gezielte Anpassung von Materialzusammensetzung und Verstärkungsmustern können spezifische Eigenschaften wie hohe Zug- und Druckfestigkeit, geringes Gewicht, Korrosionsresistenz, ausgezeichnete thermische Beständigkeit sowie faserorientierte Festigkeit erreicht werden. Faserverbundwerkstoffe sind daher besonders gefragt in Branchen wie der Automobilindustrie, Luft- und Raumfahrt, Medizintechnik und weiteren Sektoren, die robuste, aber leichte Materialien benötigen.

Entdecken Sie die Vorteile von Faserverbund
Leichtbauweise für Energieeinsparungen
Durch die Verwendung von Faserverbundmaterialien ermöglicht Waltl Design die Realisierung von Leichtbaukonzepten, die signifikant zur Energieeinsparung beitragen. Diese Materialien reduzieren das Gewicht von Bauteilen, was besonders in der Automobil- und Luftfahrtindustrie zu niedrigeren Energiekosten führt.
Hohe Stabilität und Korrosionsbeständigkeit
Faserverbundwerkstoffe bieten eine außergewöhnliche Stabilität und sind resistent gegen Korrosion. Diese Eigenschaften gewährleisten eine längere Lebensdauer und geringere Wartungskosten für Produkte, die unter extremen Bedingungen eingesetzt werden, wie in der Marine- und Chemieindustrie.
Dreidimensionale Abformungen möglich
Die Flexibilität von Faserverbundwerkstoffen erlaubt es Waltl Design, komplexe dreidimensionale Formen zu fertigen. Dies eröffnet neue Designmöglichkeiten und ermöglicht die Herstellung von Komponenten, die mit traditionellen Materialien schwer umsetzbar sind.
Nachhaltige und effiziente Produktion
Waltl Design setzt auf nachhaltige Produktionsprozesse, die den Einsatz von Ressourcen minimieren und Emissionen reduzieren. Die Effizienz der Faserverbundtechnologie trägt dazu bei, dass weniger Abfall produziert wird und die Fertigung energieeffizienter ist.
Ablauf der Faserverbundfertigung bei Waltl Design
Schritt 1: Erstellung der Negativ-Form (Urform):
Anhand von Zeichnungsdaten wird eine präzise Negativ-Form erstellt. Dieser entscheidende Schritt im Faserverbundprozess stellt sicher, dass das Endprodukt die gewünschten Spezifikationen und Qualitätsstandards erfüllt.
Die Formen werden meist mittels CNC-Fräsen oder Drehen gefertigt. Diese modernen Fertigungstechniken ermöglichen eine hohe Präzision und Wiederholgenauigkeit, was besonders bei komplexen Geometrien von Vorteil ist.
Dank unseres umfangreichen Netzwerks können wir Ihnen diese Dienstleistungen ebenfalls anbieten. Wir arbeiten mit erfahrenen Partnern zusammen, um Ihnen die bestmögliche Qualität zu gewährleisten.
Materialien der Negativ-Formen:
Die Negativ-Formen werden aus verschiedenen Materialien gefertigt, die je nach Anwendung und Anforderungen ausgewählt werden. Häufig verwendete Materialien sind:
- Ureol: Ein einfach zu bearbeitendes Material, das sich besonders für Prototypen und Kleinserien eignet.
- Polyurethan: Bietet eine gute Balance zwischen Festigkeit und Bearbeitbarkeit.
- Aluminium: Ideal für Anwendungen, die eine hohe Präzision und Haltbarkeit erfordern.
- Stahl: Wird verwendet, wenn maximale Festigkeit und Langlebigkeit gefragt sind, besonders bei großen Serien und stark beanspruchten Formen.
Dieser strukturierte Prozess stellt sicher, dass jede Komponente des Faserverbundmaterials präzise und effizient hergestellt wird, was letztendlich zur hohen Qualität und Leistungsfähigkeit des Endprodukts beiträgt.
Alternative: Erstellung einer Form von einem Positiv-Modell:
Alternativ kann eine Form von einem Positiv-Modell erstellt werden. Dieses Positiv-Modell kann entweder geliefert oder bei uns im Hause gefertigt werden. Diese Methode ist ideal, um verschiedene Tests durchzuführen. Das Positiv-Modell dient dabei zunächst als Prototyp, bis die verschiedenen Testreihen abgeschlossen sind. Dies ermöglicht eine flexible Anpassung und Optimierung, bevor die endgültige Negativ-Form erstellt wird.
Durch diese beiden Ansätze stellen wir sicher, dass jede Komponente des Faserverbundmaterials präzise und effizient hergestellt wird, was letztendlich zur hohen Qualität und Leistungsfähigkeit des Endprodukts beiträgt.
Diese Positiv-Modelle werden dann gescannt und mittels CNC-Technik umgesetzt. Alternativ kann im Faserverbundverfahren eine Direktabformung durchgeführt werden.
Schritt 2: Verwendung von verstärkenden Fasern und einer Matrix
Der nächste Schritt im Faserverbundverfahren beinhaltet die Auswahl und Kombination von verstärkenden Fasern und einer Matrix. Die Fasern, wie Kohlenstoff- oder Glasfaser, werden zusammen mit einer Matrix aus Polymerharzen, welche als Klebstoff und Füllstoff dienen, eingesetzt. Diese Materialien werden sorgfältig ausgewählt, um die gewünschten mechanischen Eigenschaften und die Haltbarkeit des Endprodukts zu optimieren.
1. Handlaminieren
- Handlaminieren ist eine traditionelle Methode, bei der Verstärkungsfasern manuell in eine Form eingelegt und mit Harz getränkt werden.
- Vorteile: Kostengünstig, flexibel, ideal für kleine Serien und Prototypen.
- Nachteile: Zeitaufwendig, Qualität hängt stark von der handwerklichen Geschicklichkeit ab.
2. Vorteile des Vakuumsackverfahrens:
- Hohe Bauteilqualität: Durch das Vakuum werden Lufteinschlüsse minimiert und eine gleichmäßige Harzverteilung sichergestellt.
- Kontrollierte Harzmenge: überschüssiges Harz wird entfernt, was zu einem optimalen Faser-Harz-Verhältnis führt.
- Flexibilität: Geeignet für die Herstellung von kleinen und mittelgroßen Bauteilen mit komplexen Geometrien.
- Kosten: Im Vergleich zu anderen Methoden wie dem Autoklavverfahren, Prepreg-Verfahren oder oder Vakuuminfusion, sind die Investitionskosten geringer.
3. Vakuuminfusion
- Bei der Vakuuminfusion werden Trockenfasern in eine Form gelegt und mit einer Vakuumfolie abgedeckt. Das Harz wird dann durch Unterdruck in die Fasern gezogen.
- Vorteile: Hohe Faseranteile möglich, gute Kontrolle über Harzverteilung, geeignet für große Bauteile.
- Nachteile: Erfordert spezielle Ausrüstung und sorgfältige Vorbereitung.
Schritt 3: Formgebung mittels Negativ-Form
In diesem Schritt werden die vorbereiteten Fasern und Harze in eine Urform eingelegt, die die genaue Form des zu fertigenden Bauteils widerspiegelt. Diese Methode ermöglicht eine präzise und reproduzierbare Formgebung, die für die Herstellung komplexer Geometrien ideal ist. Der Prozess erfordert präzise Kontrolle über Temperatur und Druck, um sicherzustellen, dass das Harz gleichmäßig verteilt wird und die Fasern korrekt ausgerichtet sind.
Schritt 4: Fertigung der Bauteile in der Negativ-Form
Nach der Formgebung härtet die Matrix in der Urform aus, wodurch das Verbundmaterial seine endgültige Form und Festigkeit erhält. Dieser Vorgang kann durch Wärmebehandlung beschleunigt werden, um die chemischen Reaktionen, die zur Aushärtung führen, zu unterstützen. Nach dem Aushärten wird das Bauteil aus der Form entfernt und durchläuft gegebenenfalls weitere Nachbearbeitungen wie Schneiden, Bohren oder eine Oberflächenveredelung.
Die 6‑stufige Waltl-Design-Methode: Der Weg zu Ihrem perfekten Produkt
Gewinnen Sie Kenntnisse darüber, wie wir in 6 Schritten aus Ihrer ersten Idee ein serienreifes Produkt entwickeln. Das 6‑stufige Rundumpaket bietet Ihnen eine individuelle Beratung in allen Phasen und hilft Ihnen, externe Kosten einzusparen.
Mehr Erfahren Kontakt aufnehmenJedes Projekt ist anders – und genau darin liegt unsere Stärke.
Mit einem breiten Spektrum an Fertigungsmöglichkeiten und einem Gespür für individuelle Anforderungen entwickeln wir Lösungen, die wirklich passen. Schnell, flexibel und persönlich.
Häufige Fragen zum Faserverbund
Was sind Faserverbundwerkstoffe?
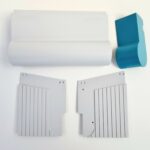
Faserverbundwerkstoffe (engl. Composite Materials) bestehen aus zwei Teilen: Fasern und einer Matrix (z. B. Harz). Die Fasern – meist Carbon (CFK) oder Glas (GFK) – geben Festigkeit und Steifigkeit. Die Matrix verbindet die Fasern und verteilt die Belastung. Durch diese Kombination entstehen leichte, stabile und langlebige Bauteile. Deshalb sind Faserverbundwerkstoffe heute in Luftfahrt, Automobilbau und Medizintechnik weit verbreitet.
Welche Arten von Fasern werden in Faserverbundwerkstoffen verwendet?
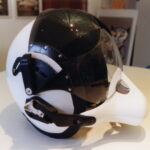
In Faserverbundwerkstoffen kommen verschiedene Fasern zum Einsatz, je nach gewünschter Eigenschaft:
Kohlenstofffasern (CFK): sehr leicht, hohe Festigkeit und Steifigkeit, ideal für Luftfahrt und Automotive.
Glasfasern (GFK): preiswert, gute Festigkeit, vielseitig einsetzbar in Maschinenbau und Gehäusen.
Aramidfasern (AFK, z. B. Kevlar): extrem zäh und schlagfest, oft in Schutz- oder Sportausrüstung genutzt.
Naturfasern (z. B. Flachs, Hanf): nachhaltig und umweltfreundlich, weniger leistungsfähig, aber für ökologische Anwendungen interessant.
Welche Matrizenmaterialien werden in Faserverbundwerkstoffen verwendet?
Die Matrix (das „Klebeharz“ im Faserverbund) hält die Fasern zusammen und schützt sie. Am häufigsten werden eingesetzt:
Epoxidharze: sehr fest, langlebig, hohe Beständigkeit gegen Feuchtigkeit und Chemikalien → Standard in Luft- und Raumfahrt sowie im Automobilbau.
Polyesterharze: preiswert und leicht zu verarbeiten, jedoch weniger leistungsfähig als Epoxidharze → häufig in Gehäusen oder Freizeitprodukten.
Vinylesterharze: gute Chemikalienbeständigkeit und stabiler als Polyester, etwas teurer → geeignet für Maschinenbau und technische Anwendungen.
Durch die Wahl des richtigen Harzes (Matrix) lassen sich Faserverbund-Bauteile optimal an den Einsatzzweck anpassen.
Was sind die Vorteile von Faserverbundwerkstoffen?
Faserverbundwerkstoffe (CFK, GFK) bieten viele Vorteile gegenüber Metallen oder reinem Kunststoff:
Leicht & stark: sehr hohe Festigkeit und Steifigkeit bei geringem Gewicht → wichtig für Luftfahrt, Automotive und Medizintechnik.
Korrosionsbeständig: langlebig auch in aggressiven Umgebungen, z. B. Chemie oder Offshore.
Designfreiheit: komplexe Formen und filigrane Geometrien möglich, die mit Metall schwer oder teuer wären.
Isolierend: gute thermische und elektrische Isolierung → ideal für Technik und Elektronik.
Damit verbinden Faserverbundwerkstoffe Leichtbau, Langlebigkeit und Flexibilität – perfekt für Prototypen und Serienfertigung.
In welchen Branchen werden Faserverbundwerkstoffe verwendet?
Faserverbundwerkstoffe wie CFK (Carbonfaser) und GFK (Glasfaser) sind heute in vielen Branchen Standard:
Luft- und Raumfahrt: für tragende Strukturen, Rumpf- und Tragflächen – Gewichtseinsparung ist hier entscheidend.
Automobilindustrie: für Karosserie- und Strukturteile, um Fahrzeuge leichter, effizienter und sicherer zu machen.
Medizintechnik: in Prothesen und orthopädischen Geräten, weil Faserverbund leicht, stabil und gut anpassbar ist.
Sport & Freizeit: in Fahrrädern, Tennisschlägern oder Golf-Clubs – für Höchstleistung bei geringem Gewicht.
Damit decken Faserverbundwerkstoffe den Bogen von Hightech-Branchen bis zu Alltagsprodukten ab.
Wie werden Faserverbundwerkstoffe hergestellt?
Handlaminieren: Harz wird manuell auf die Fasern aufgetragen – flexibel, gut für Einzelteile und Prototypen.
Vakuuminfusion: Harz wird mithilfe eines Vakuums gleichmäßig in die Fasern gezogen – für präzisere Bauteile.
Pressverfahren: Fasern und Harz werden in eine Form gelegt und unter Druck ausgehärtet – ideal für Serienfertigung.
Prepregs: vorimprägnierte Fasermatten (CFK/GFK), die im Ofen oder Autoklav gehärtet werden – hohe Qualität, häufig in Luftfahrt.
Pultrusion: kontinuierlicher Prozess für Profile, Stäbe oder Platten – wirtschaftlich bei Serien.
Autoklavverfahren: Aushärtung unter Druck und Temperatur – Premium-Verfahren für sehr belastbare Hightech-Bauteile.
So lassen sich vom Prototyp bis zur hochwertigen Serienfertigung unterschiedlichste Faserverbundbauteile herstellen.
Was sind die Herausforderungen bei der Verwendung von Faserverbundwerkstoffen?
Kosten: Die Herstellung ist oft teurer als bei klassischen Materialien wie Stahl oder Aluminium.
Aufwendige Verarbeitung: Verfahren wie Autoklav oder Vakuuminfusion sind technisch anspruchsvoll und erfordern Erfahrung.
Recycling: Die Trennung von Fasern und Matrix ist komplexer als bei reinen Metallen oder Kunststoffen.
Anisotropie (Richtungsabhängigkeit): Die Festigkeit ist nicht in alle Richtungen gleich, was eine sorgfältige Konstruktion erfordert.
Wir beraten unsere Kunden offen über diese Punkte – und entwickeln Lösungen, bei denen die Vorteile von CFK und GFK klar überwiegen.
Welche Bezeichnungen gibt es für Kohlefaser – Verbundwerkstoffe
Antwort:
Für CFK (Carbonfaser-Verbundwerkstoffe) gibt es viele Bezeichnungen – in Deutsch und Englisch:
Deutsch: Kohlefaser, Carbonfaser, Karbonfaser, Kohlenstofffaser.
Für das Material selbst: Kohlenstofffaser-Verbundwerkstoff, Carbonfaser-Kunststoff-Verbund, kohlenstofffaserverstärkter Kunststoff, Karbon-Verbundwerkstoff, Karbonfaser-Verbund, Kohlefaser-Verbund.
Englisch: Carbon Fiber, Carbon Fiber Reinforced Polymer (CFRP), Carbon Fiber Composite, Carbon Fiber Reinforced Plastic.
Alle Begriffe meinen letztlich dasselbe: einen leichten, sehr stabilen Verbund aus Kohlefasern und Harz. Unterschiede entstehen vor allem durch Sprache, Fachgebiet oder Tradition.
Warum sollten Sie Faserverbundteile mit uns realisieren?
Antwort:
Wir kombinieren Erfahrung in der Verarbeitung von CFK und GFK mit flexiblen Fertigungsverfahren. Ob Prototyp, Vorserie oder Serienfertigung – wir liefern leichte, stabile und langlebige Bauteile. Dank unseres Netzwerks können wir neben eigener Fertigung auch 3D-Druck und Spritzguss über Partner anbieten.
Unsere Kunden aus Luft- und Raumfahrt, Automobilbau, Medizintechnik und Maschinenbau schätzen die enge Beratung, kurze Wege und die Produktion in Deutschland.
👉 Jetzt Projekt anfragen und die Vorteile von Faserverbund nutzen.
Weitere Verfahren aus einer Hand – direkt bei uns oder über ausgewählte Partner.
Gute Gründe für Faserverbundlösungen!
Interessiert an unseren Faserverbundlösungen? Unser Team steht Ihnen mit umfassender Beratung und erstklassigem Service zur Seite. Lassen Sie uns gemeinsam Ihre Ideen verwirklichen.
Nehmen Sie jetzt Kontakt mit uns auf!
Zum Kontaktformular